In the first ten days of October, the chief engineer of Zhengheng power went to Switzerland with a group of 5 members of the engine cylinder hole coating technology team to complete the pre acceptance of the engine cylinder hole plasma spraying equipment to be settled in Zhengheng power. In the process of acceptance, the teamdeeply studied the process flow, key points, process control and coating performance analysis of cylinder hole plasma spraying, and won the unanimous recognition and appreciation of American technology experts!
(SUMEBore ® Coating process learning and Practice)
SUMEBore ® The coating process is to use the atmospheric plasma spraying process to coat the powdered materials on the inner surface of the cylinder, and select different spraying powders to achieve the goal of low friction, low fuel consumption, high wear resistance and high corrosion resistance. In short, it is an inner hole spraying process. This technology has already been mature in foreign countries, such as Bugatti, Porsche, Aston Martin, Volkswagen, Audi and other automobile engines, Scania truck and other diesel engines and Rotax and other motorcycle engines.
(SUMEBore ® Wide application of coating technology)
Another important application of this technology is to remanufacture waste engines and cylinder liners. Remanufacturing is different from maintenance. It belongs to green manufacturing, which can maximize the residual value of products and has great development potential!
The cylinder bore coating forms an open and dispersed porous surface after honing. It is these smooth and round holes that reduce the exposed area of fuel in the combustion chamber and piston ring; At the same time, it reduces the tangential force of the oil scraper ring, makes the piston ring enter the hydrodynamic state more smoothly, and significantly reduces the friction resistance and wear; So as to further reduce the possibility of oil consumption and gas channeling. SUMEBore ® The special porous surface oil storage structure will not be polished off in the honing process like the reticulated structure of flat top honing process. With the working wear, when the coating thickness decreases gradually, new lubrication holes will appear on the coating surface to ensure the sustainability of performance. In addition, after honing, the thickness of the coating is between 120-150 microns. Compared with the cast iron cylinder liner, the thin-wall coating greatly improves the heat conduction between the cylinder bore and the cylinder block.
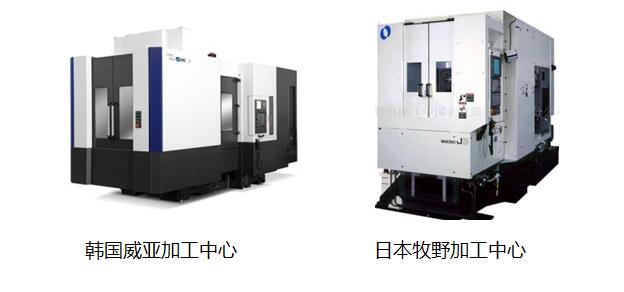
A surface reticulate morphology after honing of traditional cylinder hole
B. surface porous morphology after honing
working diagram of cylinder hole coating
As a local engine block manufacturer in China and the first company in China to introduce engine cylinder hole plasma spraying technology and equipment, Zhengheng power hopes to jointly improve the engine technical level with domestic and foreign automobile manufacturers, engine manufacturers and remanufacturing enterprises through this advanced technology and provide more services for the industry!
Post time: Nov-19-2021